Where Is The Best Wire Harness Assembly In 3d Printing Environment?
- Mefron Technologies
- Nov 17, 2022
- 3 min read
Updated: Mar 7, 2024
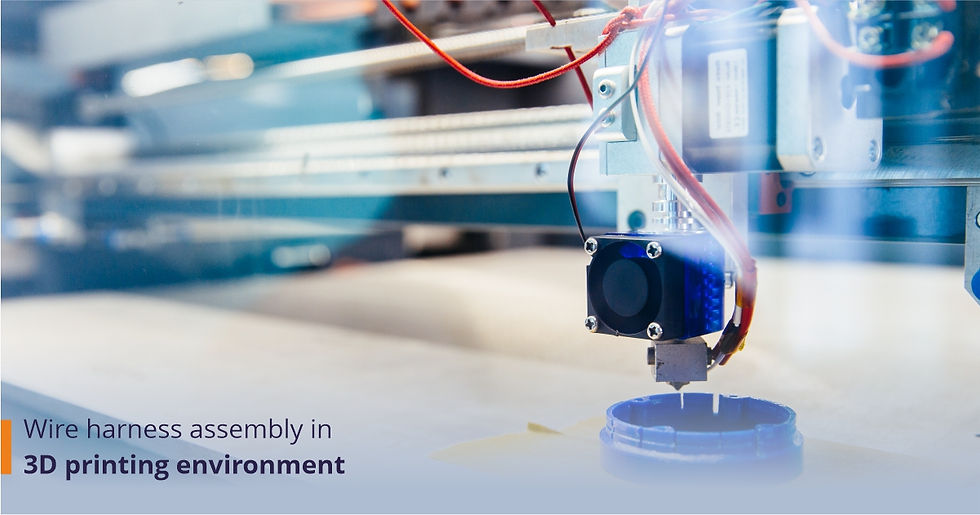
Introduction
The 3D printing process has been widely applied in the wire harness industry because it provides an efficient way to produce complex products with fine details. In fact, since the use of 3D printing technology began in 2007, many companies have started using it as a means to overcome production constraints by producing small quantities at low cost or even one-offs without having to invest large amounts of money into tooling or equipment (such as extruders). 3D printing allows companies to save money and improve profits by making their products themselves.
3D Printing as an Alternative
3D printing is a process by which objects are created by layering material in successive layers. The first layer is called the "build platform", followed by one or more support structures, then the print head that lays down material, and finally a top layer of finish or decorative material.
There are several types of 3D printers: extrusion machines (such as MakerBot), laser sintering machines (SLS), and direct metal laser sintering machines that use additive processes similar to those used for 3D printing in the industry
Current Practices in the Wire Harness Industry
Wire harness assembly is a labor-intensive process that involves assembling wire and components. It's also a difficult one, as it requires handiwork and manual dexterity to complete. In addition to being costly, it is also time-consuming, it takes about 25 minutes for each worker on average to assemble one cable harness. Sometimes, we cannot assure 100% safety in traditional harness methods.
Printed Harness Assembly

Printed assembling is a process that combines 3D printing with cable harness assembly. It allows users to create complex electronic circuits and modules on demand, which can be used in various applications including medical devices, industrial equipment, appliances, etc.
The main advantages of this technology are its simplicity and cost-effectiveness. With just one tool (3D printer), you can create complex electronic circuits or modules required by your business just by modifying existing designs or adding new components to them based on your needs.
Benefits of integrating printed harness assembly into a 3D printing environment
Reduced costs: In 3D printing, you can create your own printed cable harness at a much lower cost, with fewer resources, and at a fast turnaround.
Reduced labor cost: With 3D printing, you don't need to hire any more employees or spend more on training them; instead, you can use your existing workforce for other tasks while they assemble the wires themselves! This saves money while also allowing individuals who may not be skilled enough with traditional assembly techniques (such as welding) access to this field.
Reduced energy consumption: Many people think that 3D printing requires more energy than traditional manufacturing methods do because of its increased output rate but this isn't always true; in fact, it's quite possible for someone who knows how this technology works well enough (like me) could actually produce better results with less effort than someone else who doesn't understand what he/she's doing so well yet still has trouble getting things done efficiently sometimes despite having all sorts amazing equipment available at hand.
Conclusion
The benefits of integrating printed wire harness assembly into a 3D printing environment are many. You can have a fully functional product without having to wait for parts, which means you can get it on the market faster. And because the product is made with 3D printers, it's easier to design and make changes if needed.
I believe that the 3D printing industry has a lot of potentials to improve the wire harness manufacturing. We hope this article helped you understand how 3D plastic prints can be used as a cost-effective alternative to traditional metal cable harness assembly.
Comments